Challenge
From self-build homes to multi-million-pound developments, offices to hotels and hospitals, roads to bridges, Northern Ireland-based SDG has been partnering with contractors for over 30 years to provide products, solutions, technical expertise, problem solving and industry insights in the construction sector.
Offering over 2,000 products, SDG has a complex supply chain and looked to this AKT2I collaboration with Queens University Belfast (QUB) to progress innovation in its supply chain management.
This project set out to develop a digital representation of the current supply chain at SDG. It aimed to support data-driven decision makings such as ordering decisions and inventory decisions at SDG.
The project also set out to improve the design of the supply chain network and manage the risk of the supply chain at SDG.
The innovation was a model that enables SDG to utilise its data resources and use data-driven decision-making methods in supply chain management. There were three main needs driving innovation.
- First, SDG needs to increase operational efficiency and productivity.
- Second, SDG faces an increasingly uncertain business environment.
- Third, SDG has developed a system to analyse sales data using big data analytics, tools and techniques.
The innovation can build on the existing system and link the upstream with the downstream of the supply chain.
An AKT2I was the right vehicle for this development as it helped SDG create a tool to manage supply chains.
Outcome
A digital representation of the current supply chain at SDG was developed by the AKT2I Associate.
Data was then collected, and a simulation model created to understand the current supply chain at SDG. The AKT Associate then analysed the data by using the simulation Presentation Upload software Anylogistix.
The top 100 customers from the last 12 months were well represented on the GIS map and the greenfield analysis was conducted to analyse whether any additional warehouses should be built to best serve the current customers and where to locate the additional warehouses. Therefore, the first objective was delivered on course.
The second objective was to support the data-driven decision making such as ordering decisions and inventory decisions. A simulation model about different ordering and inventory policies was constructed and analysed to improve the design of the supply chain network and manage the risk of the supply chain at SDG.
The last two objectives were linked with the first two objectives and were delivered on course. The innovation was the supply chain model that enabled SDG to utilise its data resources and use data-driven decision-making methods in supply chain management.
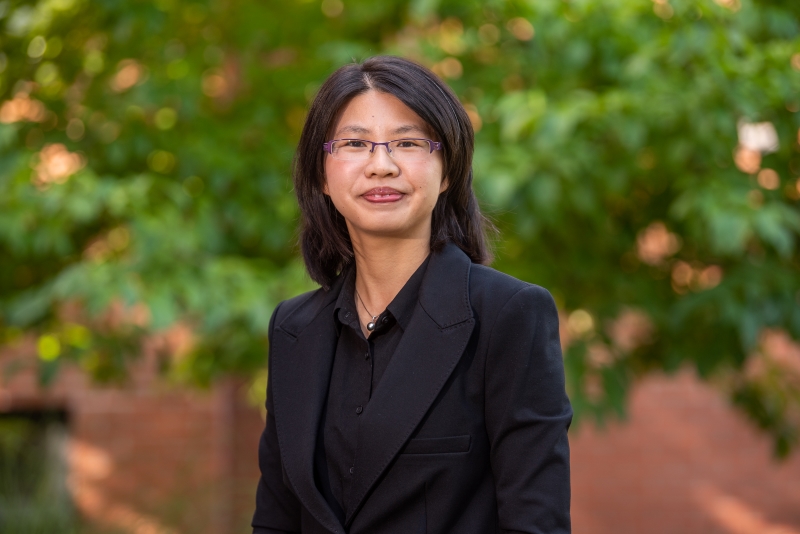
Impact
There were three main outcomes from this partnership.
The first outcome was an improved understanding of the supply chain at SDG. The product flow and information flow among the company, the company’s suppliers and the company’s customers were examined. A figure was produced to show the product flow and information flow of the supply chain.
The second outcome was the graphical presentation of the current supply chain at SDG. The results showed that most of the top 100 customers were located in Northern Ireland and the Republic of Ireland. The current SDG warehouse at Armagh served those customers very well. However, the remaining five top customers were located in England, and could be served much better by acquiring another warehouse in the location of those five top customers.
The third outcome was an innovative simulation model that examined different ordering and inventory policies for a particular product i.e., the min-max policy with safety stock, the RQ policy, and the Order on Demand policy.
This project was undertaken across one product line. The results showed that the simulation model improves inventory management and reduces total costs. It suggests that this would be rolled out across all product lines, providing a digitised data-driven supply chain. It is anticipated that a joint knowledge base and business partner relationship would work effectively in the ongoing delivery, potentially through a period of 1-2 years via a programme such as KTP.
What they say
“The graphical representation of the top customers looks amazing. The small number of customers makes big sales!”
Further information
For more information about this AKT2I partnership, please contact aoife.lynch@qub.ac.uk